Air scrubbers
Published
|Air scrubbers, scrubbers, wet scrubbers, washing towers and gas scrubbers are all names that are used interchangeably for installations that use liquid to remove unwanted substances from air or gas mixtures prior to discharge.
Applications
Air scrubbers or scrubbers, as they will be referred to here, can be used both to remove gaseous components, such as acidifying or odorous gases, and particulates/dust. They therefore have a wide range of applications and are used by many different types of enterprises.
Examples of industries where air scrubbers are commonly used:
- Waste incineration
- Wastewater treatment plants
- Biogas plants
- Fish processing industry
- Chemical process industry
- Composting facilities
- Metallurgical industry
- Food industry
- Oil refineries
- Cement production
- Wood processing industry
- Printing companies
Types of air scrubbers
There are many different types of air scrubbers. The probability of legionella bacteria becoming established will depend on a range of factors, including the properties of the (flue) gas and the liquid used in the cleaning process.
To achieve the best possible cleaning effect, designs that facilitate maximum contact between liquid and air/gas mixture are preferable. Dispersion of the liquid into small droplets or in the form of a film produces a large surface area, which helps to increase the transfer of contaminants from gas to liquid. The properties of the liquid will vary depending on which contaminants are to be removed.
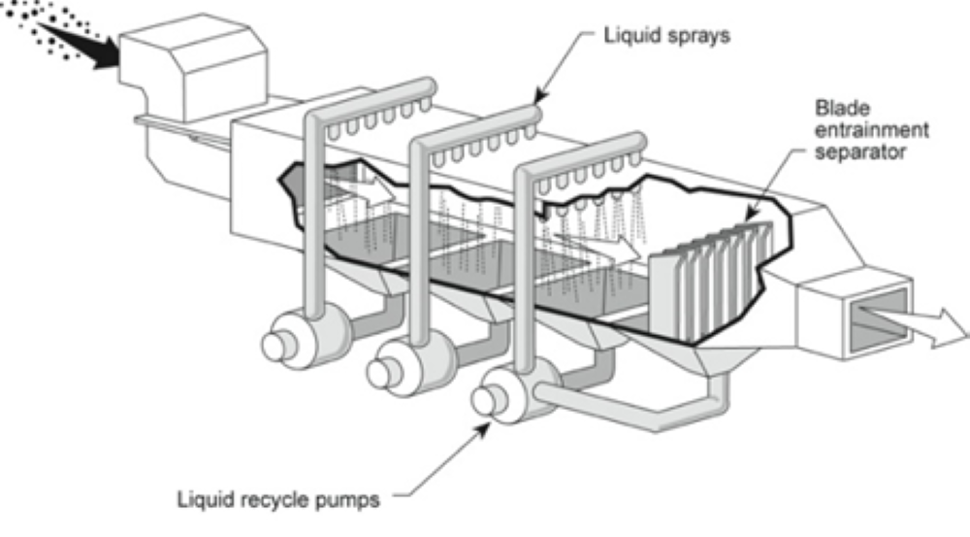
Bioscrubbers
Bioscrubbers are tower scrubbers which contain a packing material, such as plastic balls, where a microbiological flora (biofilm) is established.
Bioscrubbers are often used to remove odours by transferring the odorous components to the liquid and degrading them in the biofilm. The pH of the liquid will be within a range within which legionella bacteria can also grow.
Biofilters, also known as bark filters, are also used to reduce odours. These are widely used in the wastewater treatment sector and in the waste sector in connection with the biological treatment of organic waste. In filters of this type, contaminated air is passed through a medium which is designed to create ideal living conditions for microorganisms, which will "eat" the contaminants. In order for a biofilter to function optimally, the air should be wetted before being fed to the biofilter. The simplest systems work by inserting nozzles into the air duct before the filter. More advanced wetting systems sometimes referred to as “air scrubbers”. It is not unlikely that legionella bacteria will be able to thrive in biofilters. However, because the gas flow velocity is low, of the order of 0.02 m/s, the dispersal of bacteria into the air will be limited.
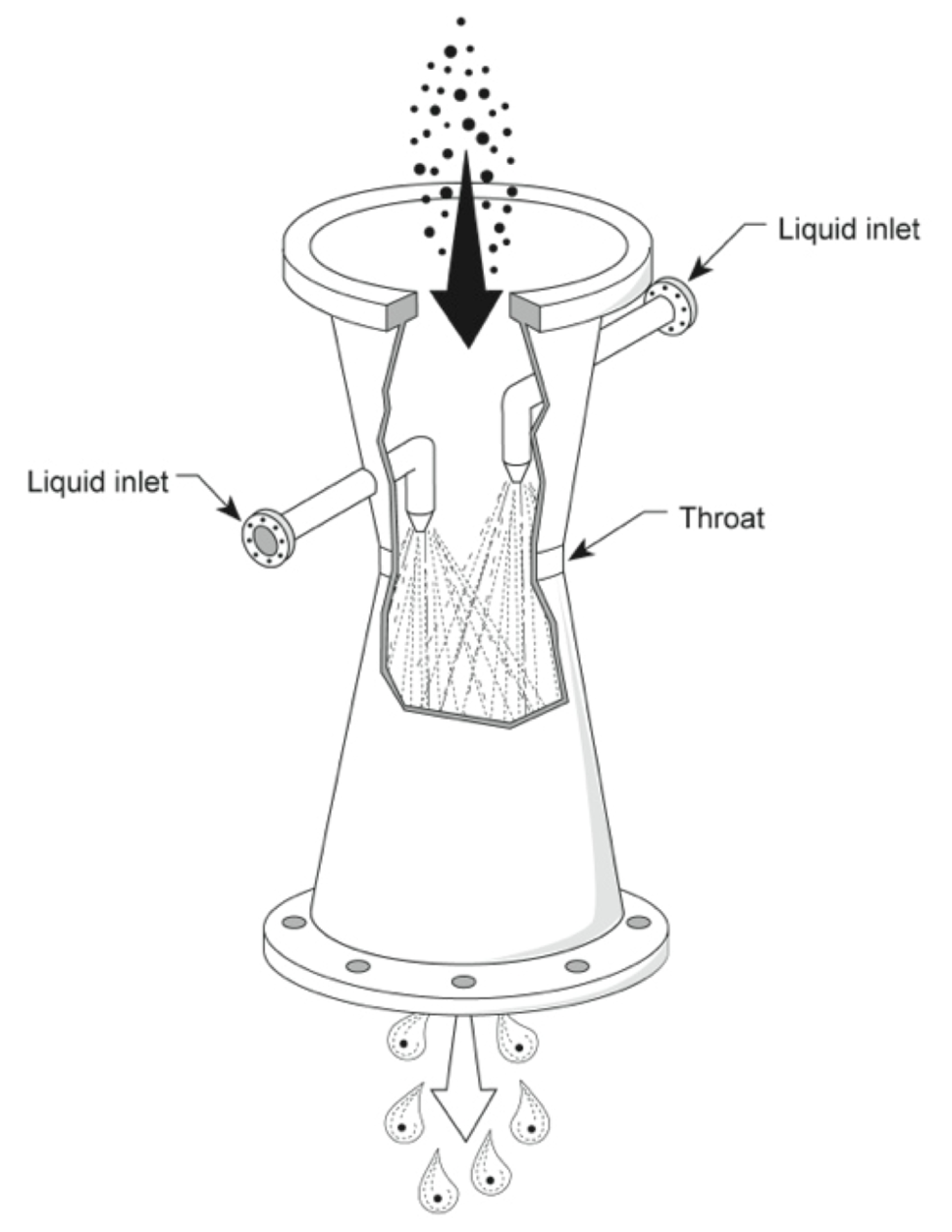
Venturi scrubbers
Venturi scrubbers consist of a converging section, a narrow throat and a diverging section. Figure 2 shows the principle of venturi scrubbers. They are designed to utilise the kinetic energy of the flue gas to disperse the scrubber liquid into fine droplets. The liquid that is added either at the entrance to the narrowest section, or at the entrance to the converging section, will be atomised due to the high gas flow velocity which is achieved when the cross-section is reduced. The contaminants are transferred from gas to liquid, and the gas velocity will decrease in the diverging section.
Venturi scrubbers can have many different process designs. They are also known as jet scrubbers.
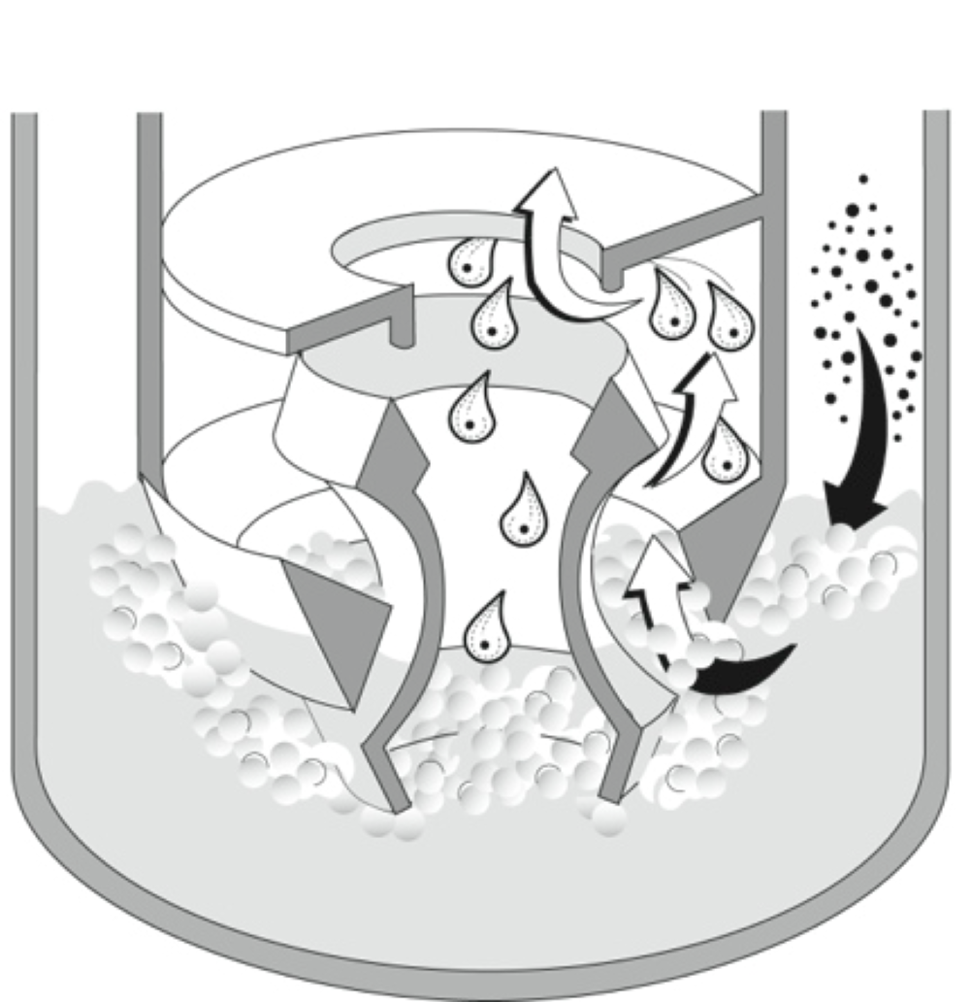
"Entrainment scrubber"
The gas is pressurised here through the liquid and fed via narrow passages in a way which causes the liquid to be entrained ("self-induced spray"). Although they can also remove gaseous components, these types of scrubbers are primarily used to remove particulates.
Figure 3 shows the principle of an entrainment scrubber.

Mist eliminators/moisture separators
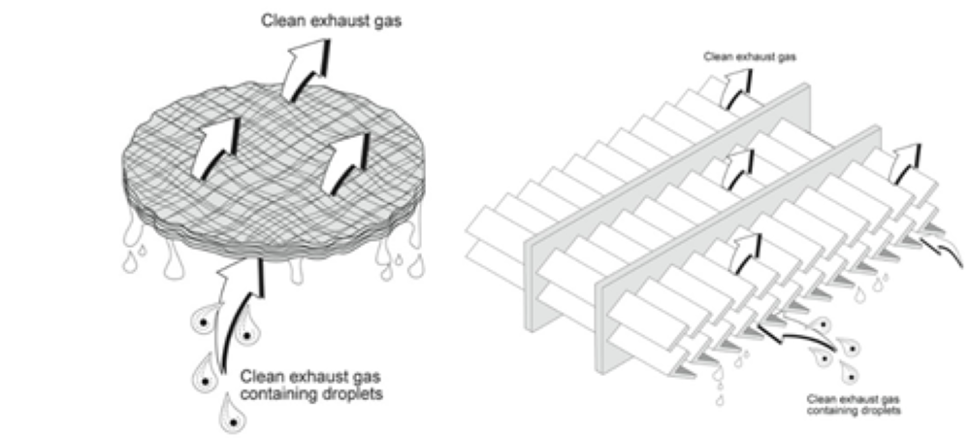
When the flue gas passes the liquid, it becomes saturated with moisture, and it will entrain droplets. Various types of mist eliminators/moisture separators are used to reduce the water content before the gas is discharged.
Examples of such separators are cyclone-shaped separators, wire meshes and leaf separators. The principles for these are shown in Figures 4 and 5.
Mist eliminators are prone to fouling.
Preventive measures
Assessing the risk of legionella growth and dispersal
As legionella bacteria occur in all fresh water, it must be assumed that favourable conditions for growth in an installation will result in such bacteria becoming established in the system. The growth conditions for legionella bacteria are described in About legionella bacteria and legionellosis and Risk mapping and preventive measures (both in Norwegian). The main risk factors for growth are whether there are zones where the liquid or wet (moist) surfaces are at a favourable temperature, and whether the bacteria have access to nutrients. The extent of fouling (biofilm), precipitation, sludge accumulation, lime deposits and corrosion products that can contribute to bacterial and amoeba growth will be of great importance when assessing the risk of legionella growth.
In addition to the risk of legionella growth, it is also necessary to consider whether there is a risk of the dispersal of aerosols which may contain legionella bacteria, including the extent to which aerosols are formed, their dispersal and whether any post-treatment of the aerosol-containing flue gases will kill or remove the legionella bacteria again. As a general rule, aerosols would be expected to form where air/gas flows rapidly past a flowing water surface or water droplets.
The growth potential of legionella bacteria in air scrubbers will vary greatly depending on various factors such as the properties of the (flue) gas and scrubber water and chemical additives, the type of scrubber, the operating schedule, and the quality of the operation and the maintenance of the facility. The chemical composition of the scrubber water will depend on the starting point of the water, the composition of the (flue) gas and what is removed from the (flue) gas. Examples include the fact that the growth conditions for legionella bacteria in air scrubbers which use seawater are normally poor, while freshwater-based air scrubbers which clean flue gases from the wood processing industry and oil refineries can have good growth conditions. Aerosol formation and dispersion conditions may also vary from facility to facility. It is therefore very important that risk assessments are carried out, both in order to characterise the risk potential and as a basis for planning preventive measures.
The basis for assessing the risk of legionella bacteria growth and for planning preventive measures, including the use of microbiological analyses, is discussed in Risk mapping and preventive measures and Microbiological analyses (both in Norwegian). For most scrubber plants, a set of analyses of legionella bacteria should be carried out to determine whether conditions are suitable for the growth of such bacteria inside the scrubber concerned. Essential documentation for possible exemption from Chapter 3 of the Regulations relating to environmental health protection is described in section "What are analyses used for?"; see Microbiological analyses. It will be possible to draw on experiences from other similar scrubbers where such empirical information is available. Currently, experiences are limited to what is referred to in the section above.
Risk assessments for air scrubbers should:
- identify whether there are any risk areas with favourable temperature conditions for legionella growth in the installation.
- assess the water quality in these risk areas and the likelihood of it leading to the growth of legionella bacteria.
- assess whether aerosols could be formed from the liquid in the installation.
- assess whether legionella-infected liquid could be transported from identified areas of legionella bacteria growth to areas where aerosols could form.
- describe the use of growth-inhibiting agents in the system and their anticipated effect, based on documentation in connection with use in this or other virtually identical installations.
- describe the scope for thorough cleaning of the relevant components of the installation, from any growth areas for legionella and the transport path of the liquid to places where aerosols could form.
- describe what has otherwise been done to prevent the growth and transfer of legionella bacteria via aerosols (existing operating and maintenance procedures, treatment methods) and the results of the measures, as well as procedures to be followed in the event of actual or suspected outbreaks.
Based on such a review, an assessment must be carried out of the need for technical changes and changes to operational and maintenance procedures. The operating and maintenance procedures, especially cleaning and disinfection, should be subject to an ongoing risk assessment, where points 5 and 6 of the above review are pivotal.
Examples of factors which are of importance in any assessment of the risk potential of an air scrubber are:
-
temperatures in parts of the system which could promote microbiological growth
-
design of the scrubber and circulation systems for scrubber water with regard to the formation of coatings/biofilm
-
hydraulic conditions which could affect biofilm formation, detachment and possibly aerosol formation
-
corrosion on surfaces which could reduce the effect of cleaning and disinfection by allowing bacteria and amoeba to gain a "better foothold" and increased nutrition
-
experience from analyses of scrubber water in relation to microbiological growth
-
treatment of the flue gas after the air scrubber which could prevent the dispersal of legionella bacteria, such as a sharp rise in temperature, filtration or disinfection. The extent to which the cleaning step will be in operation at all times, and the effect of the cleaning step, must be subject to a thorough assessment
It is important that the process through to the determination of operational and maintenance procedures ensures that those responsible in various functions become familiar with their own installation. It is therefore strongly recommended that the risk assessment be carried out and the operational plan be determined by a multidisciplinary team.
Technical design
As described previously, there are many different types of air scrubbers. However, there are also considerable differences within individual types of scrubbers.
Many major industries are struggling with biofilm formation, including the oil industry, where microbial corrosion caused by biofilm formation is a problem. The wood processing industry is also affected. Legionella bacteria have been detected in scrubbers which treat flue gases from both of these industries.
Installations must be designed so that it is possible to carry out cleaning and disinfection in all parts where legionella bacteria could grow. This includes pipes, pump housings, tanks, etc., which form part of circulation systems for process water, "process chambers" (where the cleaning process takes place) and mist eliminators/moisture separators.
Mist eliminators
Well-designed mist eliminators reduce the quantity of droplets that are released into the air. However, the mist eliminator itself could be a habitat for legionella bacteria growth and aerosol formation. There are examples of poorly cleaned mist eliminators which have led to the release of legionella bacteria from installations where no such bacteria have been found in the circulating liquid. Mist eliminators and the outside of the nozzles must be cleaned regardless of water quality if the process water contains organic matter.
Preventive treatment
Installations which are found to be capable of spreading legionella bacteria must be regularly cleaned and disinfected. Other treatment will also be relevant. Treatment methods for the prevention of legionella growth are discussed in Treatment methods. Risk assessments will form the basis for determining the scope and frequency of preventive treatment, but the installation must at least be cleaned and disinfected:
-
Immediately before the installation is put into operation for the first time
-
At least every six months
-
During or after actual or suspected outbreaks of legionellosis (NB! But only after thorough sampling)
If an installation or its components have undergone significant alterations or been opened up for maintenance, careful consideration must be given to whether legionella bacteria could have entered the installation.
Air scrubbers where the risk assessment concludes there is little or no risk, should also be cleaned regularly. Examples of cleaning steps after an air scrubber which could reduce or eliminate the spread of legionella-containing aerosols are ozone, biofilters and carbon filters. Both ozonation and biofiltration are used to remove odours at wastewater treatment, composting and biogas plants.
The growth conditions for legionella bacteria are likely to be favourable in a biofilter. In open filters, the risk of infection is probably low due to the limited dispersal of the bacteria into the air at the low air flow velocities that are used. In closed biofilter installations, the flue gases are often passed through a chimney. This leads to an increase in the air velocity, and thus also a greater risk of entrainment of aerosols which could be dispersed to the surroundings.
Microbiological control and monitoring
HPC and legionella analyses will be useful for reference purposes when assessing the effects of operational and maintenance procedures. It is recommended that monthly analyses of both colony counts (HPC) (36 oC) and legionella bacteria are carried out during the first year after the introduction of new procedures.
Microbiological analyses are described in Microbiological analyses. The purpose of microbiological analyses is to verify that the established operating and maintenance procedures are satisfactory. The scope of analyses and the choice of analytical parameters will vary depending on a number of factors, including knowledge regarding the effectiveness of the chosen treatment method and experience gained from an installation.
Because the thermal and chemical conditions in the water phase in an individual air scrubber are affected by the properties of the exhaust gases being purified and the liquid medium that is used, it is impossible to specify action levels based on colony count analyses. The uncertainty surrounding the interpretation of numerical values from analyses, be it colony counts or legionella analyses, indicates that owners must have a sound knowledge of the microbiological conditions in their own installations.
Chapter 3a, Section 11 of the Regulations relating to environmental health protection requires microbiological sampling to be carried out at least once a month unless it can be documented that the growth and dispersal of Legionella cannot occur. The purpose of a sampling and analysis programme which includes both colony count and legionella analyses is to provide the best possible reference basis for assessing the effect of future operational and maintenance procedures.
It is recommended that monthly analyses of both colony counts (HPC) at 36 oC and legionella bacteria are carried out during the first year after the introduction of new procedures. Legionella spp. should be used as an indicator parameter for the possible growth of all types of legionella bacteria, because the detection of one species of legionella does not preclude the growth of other species in the same system.
It would make sense to also analyse for Legionella pneumophila serogroup 1 if the presence of Legionella spp. is detected, because it is considered to be one of the most contagious variants. The detection of this will make the implement of measures more urgent. Samples of both liquid and biofilm should be taken from areas where growth conditions are most likely to be favourable.
In the event of an actual or suspected outbreak, samples should be taken as part of the process of mapping the outbreak for analysis of legionella bacteria. The samples must be taken prior to cleaning and disinfection.
In the event of an actual or suspected outbreak, samples should be taken as part of the process of mapping the outbreak. Samples must be taken both from the water phase and from damp surfaces where water droplets could become detached and entrained in the air. The samples must also be taken prior to cleaning and disinfection.
Procedures for operation and maintenance
The established operating and maintenance programme, including procedures for control, monitoring, cleaning and biocide/heat treatment to prevent legionella growth, must form part of the internal control process within the company.
Amongst other things, the operating and maintenance programme must describe:
-
control parameters that are relevant to legionella growth/dispersal
-
control parameters that are relevant to control of the scrubber, any water treatment and other relevant processes
-
the components that require routine cleaning, disinfection and supervision in general
-
time interval for the checking of components/wires, etc. in accordance with the risk assessment
-
assessment criteria to determine when measures must be implemented, and procedures for the implementation of measures.